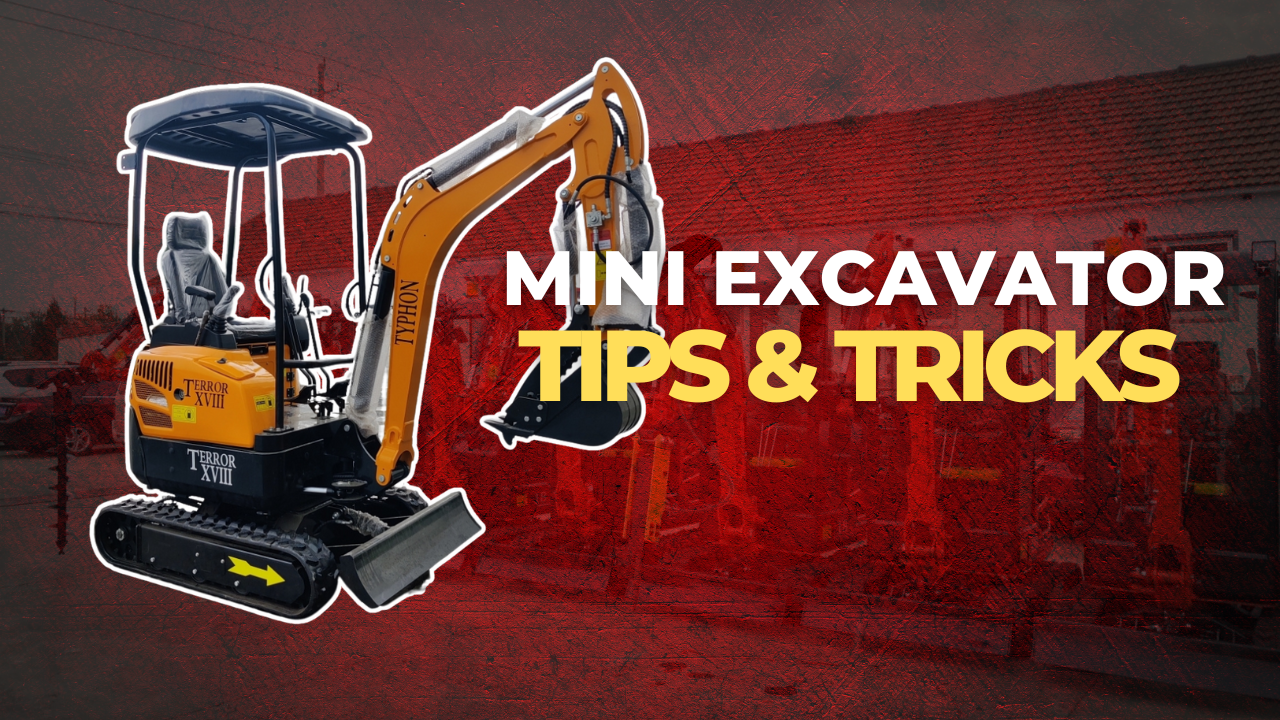
Mini Excavator Tips & Tricks for Operation and Maintenance
Mini excavators are increasingly being utilized in the construction and landscaping industries. Conventional excavators fall short in terms of flexibility, compatibility, and overall efficiency when compared to these compact machines. Experts are progressively utilizing mini excavation techniques for trenching and site preparation.
Achieving success in these fields depends on knowing about mini excavation techniques. Strong excavation techniques help professionals in building, contractors, and do-it-yourselfers. Learning mini excavators guarantees safety, increases output on projects, and improves efficiency. Correct method utilization may assist in reducing expensive excavation errors and saving time.
Dealing with Mini Excavators
Their size and flexibility make them different from excavators. The 1–10 ton machines are suitable for tiny areas where the bigger equipment cannot function. Their mini size lets operators enter residential areas or narrow paths without destroying property. Zero-tail swing technology and other innovative design aspects allow the mini excavator to operate in tight spaces with full mobility.
Projects need various mini excavators. Some designs have long landscaping and utility trenching arms. Others are suitable for construction heavy lifting. Choose the right engine and hydraulic system for your project since they effect performance.
Small-scale excavation has various benefits. Running costs are lower for smaller machines since they require less fuel. Contractors can readily complete tasks using buckets, augers, and grapples. Mini excavators clean sites and dig foundations with little effect.
Knowing mini excavators’ fundamental features and operating mechanics aids DIYers and building professionals. These little tools improve excavation accuracy and efficiency in commercial site development and household renovations.
Critical Mini Excavation Methods
Project success requires small-scale excavation strategies. Operators have to understand attachments, bucket angles, and excavation depth. Changing the bucket angle enables one to achieve the intended grade without compromising stability and helps to remove material in confined places simpler. These simple strategies raise productivity and reduce losses.
Mini excavator operators must also watch for typical errors. Overextending the excavator arm may cause instability or tipping. Misalignment during excavation is common due to poor ground personnel communication. These blunders harm projects and site safety. Knowing these hazards helps operators operate prudently.
Methodical planning and excavation are needed. Operators should assess site conditions and mark reference points before starting work. This method fits project requirements and regulates excavation depth. A methodical digging pattern from one end of a job site to the other ensures consistent results. These methods increase performance and speed backfilling by improving material placement after excavation.
Optimal Results: Trenching Techniques
Mini excavation requires trenching for foundation. Trenching has several uses. Utility installations like subterranean lines benefit from open-cut trenching. Bench trenching retains vertical walls and provides a wider surface base in unstable terrain. Know when to apply these tactics to save time and money on projects.
Right trench depth and breadth are key to mini-excavation success. Project requirements like pipe widths and environmental conditions affect these traits. A frequent gardening need is a depth that decreases water collection and increases drainage. Make sure the ditch width allows equipment attachments without damaging surroundings or buildings.
Mini excavators must follow safety guidelines for each excavation. This requires understanding subterranean utilities and risky terrain and checking site conditions before commencing work. Effective ground crew communication ensures safety and maximum production. Using proper PPE during trenching may improve worker safety.
Mini excavation abilities may be improved by learning trenching procedures, dimensions, and safety. Reviewing these principles can assist improve knowledge and promote correct standards on all projects, fostering repeat business and pleased customers.
Simplified Backfilling Strategies
Backfilling comes in a somewhat important stage after excavation. The excavated area supports building or restores the ground. Before backfilling, operators must assess the site and material needs. Clean up the trench and dirt. The new fill material is cleaned and compacted.
Choose backfilling materials based on project requirements and functionality. I utilize gravel, sand, and natural soils. Water-sensitive areas use gravel because it drains well. Thin layers of compacted sand fill may sustain high weights. To enhance compaction, lay backfill no thinner than 12 inches.
Perfect results need backfill compaction. Guaranteed fill area density using mechanical compactor or vibratory plate Guidelines provide 90–95% of maximum dry density. Check your work regularly for spots that require further compaction before settling.
Backfilling requires site prep. Avoid errors by marking utilities and risks. Dry days improve backfill placement by preventing rainwashing. These principles assist operators in improving project results, safety, and efficiency.
Choosing the Correct Supporting Materials
Mini excavators work best with the correct attachments. Thumbs, augers, hydraulic hammers, and buckets are popular. Each kind has a particular function and may affect project success. While trenching buckets are for small trenches, general-purpose buckets are fit for excavating and transporting materials. Understanding these attachments enhances your knowledge and facilitates the transition of project tools.
Consider project scope, soil conditions, and material handling before choosing attachments. A heavy-duty bucket or rock auger increases performance in rocky or compacted soil. Custom buckets aid precise digging. Always match attachment size to mini excavator specifications for safety and performance.
Specific attachments may boost work efficiency. Grading blades enhance landscaping accuracy and reduce handwork. Hydraulic hammers accelerate destruction safely. By employing the right attachments, operators may improve their mini excavation procedures and outcomes.
Safety Procedures Operating Mini Excavators:
Mini excavators need safety training and certification. Training ensures operators understand equipment capabilities, limits, and safety. The certification procedure allows safe passage across dangers. Aware workers seek safer workplaces. Many construction sites require heavy equipment operators to show training.
Employee safety is improved by proper gear. Wear sturdy helmets, steel-toed boots, safety goggles, and high-visibility gear. Employees should wear gloves that grip controls without losing dexterity. This gear makes operating the mini excavator or unexpected movements safe.
Without proper protection, minor accidents might cause serious injuries or long-term health consequences. Before excavating, secure the site area. To prepare a location, remove obstructions and clarify duties.
Every day, check tools before starting work. We look at lights, brakes, fluids, and other crucial signs. Clear team communication helps to reduce task and schedule errors, therefore enhancing safety. Establishing equipment paths helps to improve output by lowering traffic in congested areas and thereby lowering accidents.
Safety measures safeguard workers and boost project efficiency. Safety promotes trust between team members and contractors and puts well-being above speed. Companies gain respect by investing in safety and training.
Modern Methods for Experienced Workers
Experience helps mini excavation operators to become more accurate and efficient Without sacrificing accuracy, smooth, under-control actions may increase speed. Using feathering the controls, operators may make little adjustments to ensure a clean excavation. By focusing on perfect digging and moving soil transitions, skilled workers may decrease interruption and increase output.
Mini excavators experienced operators also have to troubleshoot. Mixed soils and uneven ground complicate excavation. Changing the bucket tilt will aid while working in hard-packed soil. Use the appropriate attachment, such as a ripper tooth for uneven ground, to overcome these challenges. Knowing these elements helps to avoid downtime and enhance processes.
Slope work and demolition need for special techniques for success and safety. Top-down work addressing slopes helps to avoid landslides and equipment tipping. Equipment should be level whenever at least reasonably practical while working on slopes or stabilizing before excavation. Demolition done methodically assures construction safety at all levels and provides excellent trash management.
Advanced mini excavation techniques need expertise and regular practice. Training in constant accuracy may enable scaling operational speed without compromising quality. Every project has different issues; hence exchanging knowledge with colleagues in the sector enhances future performance.
Expert Advice: Always Useful
Every professional should learn the fundamental mini excavation techniques covered in this text somewhat well. We covered the importance of understanding mini excavators, proper trenching and backfilling methods, and the attachment option. Safety measures and modern techniques provide operators the tools they need to succeed on the job site.
Frequent use of these techniques will help you develop your skills. One should never cease investigating and learning in the perpetually shifting terrain of excavation. Dedicated to broadening your knowledge will enable you to become more efficient in addition to providing a superior job. Apply these methods to examine how your ability grows in accordance with project success.