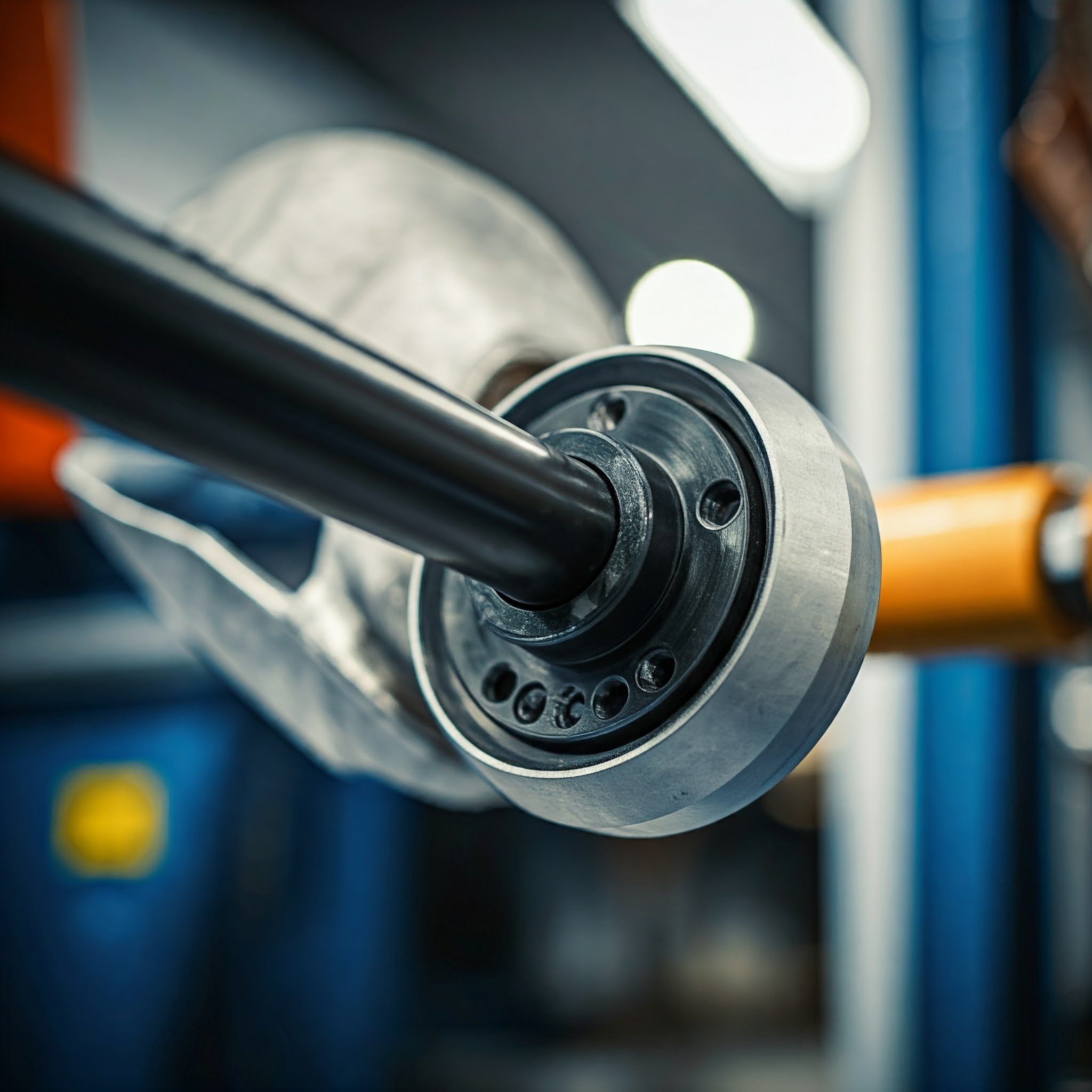
8 Important Equipment Undercarriage Maintenance Tips
The undercarriage of large machinery is very vital. The optimal performance and lifetime of your equipment depend on frequent maintenance, even with so many moving components. On the underside of heavy machinery, you may usually locate some of the initial wear and tear indicators.
Taking care of your equipment will help you avoid needless downtime and save a lot of money. Find more about the advantages of keeping the undercarriage of your equipment intact.
The Importance of Undercarriage Maintenance
Operating machinery, especially outside, is your obligation as the operator to keep each piece so that it runs as long as it should. Benefits of undercarriage maintenance include:
- Safety: Frequent undercarriage maintenance helps you to solve problems and take care of difficulties before they endanger safety. Monitoring your equipment helps you to run in more safe conditions and lowers the possibility of malfunctions and mishaps. Keep your undercarriage neat and well-maintained to avoid both possible environmental risks from fluid leaks and endangering other workers.
- Minimal repairs: By carefully inspecting and maintaining your machinery, you can avoid many costly repairs and component replacements. Everything from refilling your fluids to undercarriage cleaning can help reduce the need for repairs.
- Better performance: Parts that are too worn-out or contaminated could affect the operation of your equipment. By routinely handling maintenance, you help to minimize performance problems.
- Sustained value: Maintaining the value of your equipment depends on keeping the undercarriage in optimal shape. A well-maintained undercarriage will increase resale values and ensure flawless operating of your bike.
8 Top Equipment Undercarriage Maintenance Tips
Great maintenance of your machines has so many advantages. Use the following eight suggestions if you wish to extend the life and keep your equipment functioning efficiently by better maintaining the undercarriage:
1. Clean the Undercarriage Daily
Having personnel clean the undercarriage of their equipment at the conclusion of each workday may be a wonderful approach to prevent unneeded downtime and problems. Eliminating trash and grime will help to slow down early wear.
Pressure washers and shovels let operators dislodge muck that can weigh the machine down and lower fuel economy. In colder climes, trash can freeze and lead to the following issues:
- Rubbed bolts
- Loose guiding
- Seized rollers
To make this procedure even simpler for operators, manufacturers have begun building newer pieces of equipment with easily clean undercarriage.
2. Routinely Inspect the Undercarriage
Apart from everyday maintenance, monthly undercarriage inspection of equipment may be quite helpful. By doing a thorough check, one might identify either excessive or uneven wear that, without treatment, can rapidly become expensive issues. Examining the undercarriage can help you to find missing and broken components as well as whether the tracks are out of alignment. Pay particular attention to fluid leaks as they could point to more serious problems, including roller or seal failure.
You should routinely take care of the following:
- Drive motor
- Main idlers
- Rollers
- Drive sprockets
- Track chain
- Track bolts
- Track tension
- Track shoes
- Rock guards
Another rather useful reference for your machine is the manufacturer’s handbook. Maintenance guidelines tailored especially for your equipment provide the finest available servicing advice.
3. Follow the Basics
Staying with the fundamentals is one of the finest strategies for keeping undercarriage of your equipment intact. Following training, it might be easy to overlook the basic practices for maintaining a machine in operating order.
Refer back to these simple ideas if you wish your equipment to remain in good working order:
- Go in broad circles.
- Limit your time on sloping slopes.
- Steer clear of unpleasant surroundings.
- Reduce whirling.
- Make sure your shoe widths match.
- Choose an appropriate grouser.
- Follow the correct methods of excavation.
Sometimes a refresher on selecting the finest procedures for preserving machinery calls for reviewing user manuals and safety instructions.
4. Keep Parts Greased
Every part moves better when the undercarriage is kept well-oiled. Find the grease locations on your particular machine and ensure to lubricate them at least as advised by the manufacturer. Though depending on the surroundings and scenario you operate your machines in, you could have to lubricate the undercarriage once a day or even multiple times a day. Dirt is pushed out by greased machinery, which also leaves minimal area for trash accumulation.
Maybe think about lubricating later rather than before the workday. Warmer components help grease fittings absorb oil and lubricant more effectively. Starting the workday this way might be less successful if parts are cold.
5. Maintain Proper Track Tension
Reducing needless wear and tear depends on keeping appropriate track tension. Should the tracks be very loose, you run the risk of slipping or increased wear. The stress may blow out bushings in extremely tight tracks.
Track tension should be changed for every working condition and set to manufacturer standards. The surroundings operators are operating in should be taken into consideration, as softer or muddy circumstances best fit looser tracks.
6. Fully Train Operators
Regardless of frequency of use of the equipment, every user should be aware of the best practices. Every person handling machinery should be familiar with the foundations and techniques for routine maintenance. Make sure everyone has rapid access to manuals so they may refresh themselves as required.
Better performance depends on improved driving and cleaning methods resulting from well trained personnel.
7. Get to Minimal Wear by Driving
Correct training will help operators drive their equipment in a way that enhances the undercarriage of the equipment. Avoid the following if you wish to treat your machinery the best:
- Rapid mobility
- Going backwards
- Slopes for surfaces
- rotating more times in one direction than another.
Driving to reduce wear and tear helps your undercarrier suffer less damage.
8. Swap out Worn Parts
Changing out faulty or worn-out components as soon as you find them is one of the best ways you can save equipment expenses. This stops more damage and helps the machinery run as it should.
Do not delay purchasing new components. New components are far less expensive than replacing your equipment completely, and the longer you wait, the more likely it is that more problems may surface in the interim.